- Home
- Engineering Training Programs
- Process Engineering
Process Engineering
Process Engineering Program is unique. It begins by discussing the design of processes for desired physical and/ or chemical transformation of materials.
- Competent Trainer with more than 25+ years’ experience from Engineering Field
- 100% Placement assistance
- Exposure to working culture of Engineering, Procurement and Construction Companies.
- Through Knowledge provided to understand the project activities.
- Introduction of interactive methods within the departments.
- Understand of Deliverables to function smoothly and quality output.
- Acquire the knowledge of Advance technologies used currently.
- Enrich the knowledge of International codes and standards for perfection in design.
- Enhance the knowledge of Current engineering practices used.
- Training in Personal Development to enhance the communication skills.
The Process training will equip the participants with the knowledge and skills to design efficient and effective processes. They will learn how to develop process flow diagrams, identify unit operations, optimize material and energy flows, and consider safety and environmental factors during the design phase.
The Process Engineering course prepares students to be competent professionals capable of designing, optimizing, and managing industrial processes. They are equipped with the technical knowledge, analytical skills, and problem-solving abilities necessary to address complex process-related challenges and contribute to the efficiency, safety, and sustainability of industrial operations.
Fresh/ Experienced - Diploma/ Degree in Chemical Engineering
Module I – INTRODUCTION
- Introduction to Upstream, Midstream and Downstream Industry like oil & Gas, Petrochemical, Chemical, Fertiliser, Steel, Power, Pharmaceutical, Food, Water etc…including their function and role of Chemical Process Engineer.
- Introduction to various phases in the project life cycle and role of chemical process engineer in the various phase of project to enhance skills for working.
- Introduction to process engineering department deliverables including use by various engineering department and interface requirement and impact during various stages in project execution.
- Introduction to difference between process equipment and utility equipment
- Introduction to various Static equipment used in process industry including their application like storage, heat exchange, mixing, accumulator, distillation, Separators etc…
- Introduction to Rotating equipment like Pumps, Compressor, Turbine, Blowers etc.
- Introduction to package equipment used in process industry including their applications like Boiler, Chiller, Cooling Towers, Nitrogen Separation Plant etc.
- Introduction of various Valve, Special Parts and Instruments including instrument interlocks for various processes.
- Guidelines for Equipment layout Preparation including recommended industrial practices and standards.
- Introduction to plot plan and use of plot plan by various engineering departments also forming equipment Tag Numbers
- Guidelines on Preparation on ITB and BEP and FEED based on Conduct research to develop new and improved manufacturing processes, Establish safety procedures for those working with dangerous chemicals, Develop processes for separating components of liquids and gases, Design and plan the layout of equipment, Conduct tests and monitor the performance of processes throughout production, Troubleshoot problems with manufacturing processes, Evaluate equipment and processes to ensure compliance with safety and environmental regulations, Estimate production costs for management
- Review the ITB (Invitation to Bid) documents submitted in the proposals stage, raise, technical queries, manage inputs to other disciplines, review techno-commercial, vendor offers; prepare proposal technical write-ups and man-hour estimates.
- Verification of design integrity. Use Process Simulation software such as HYSYS and PIPESIM to ensure project specification details in the FEED Packages are feasible. Interpret and evaluate reports from process engineering software. Evaluate and compare the various FEED package documents and Data Sheets using scope of supply analysis and heat-and-mass balance calculations. Identify discrepancies and inconsistencies take corrective action where required.
- Verify and conceptualize the most optimum work route. Identify a clear scope of work/supply and accordingly plan/schedule the engineering activities and manpower resource. Identify and quantify total number of engineering deliverables, man-hour allocation, format of delivery, time schedules and other requirements for execution of the work.
- Establishing a process design basis, developing process options and optimization of selected design.
- Preparing bid and purchase specifications for processing equipment (e.g. pressure vessels, exchangers, filtration skids) Generating Deliverables list and their use for each engineering disciplines.
- 3.1. Project Phase 1 – Identification Phase for Preliminary Process Design :In this phase various options for given process is identified and screening is done based on process requirement, Safe operating requirement like fully Automatic, Semi-Automatic, Manual and Batch Type, safe maintenance requirement, climatic conditions and finally economy. During Identification phase it is mandatory to focus on revenue, expenses reduction, strategic growth, improving reliability and efficiency, identifying key risk and uncertainties, and finally to maintain consistency working on searching multiple options to reach to process goal, identifying major equipment required for set process, preparation of Block Flow Diagram (BFD) and finalising approximate cost of project which includes mainly cost of equipment.
- 3.2 Project Phase 2 – Selection and Alternatives evaluation for Preliminary Process Design : Evaluation of identified process alternatives :
- Preliminary Process Design :After final evaluation work start on only one process application and further development is started for generating data as a input to further detailed engineering. Some of the deliverables generated at this stage are as follows
- Design Basis for Process at preliminary stage including scope, purpose, requirement of various inputs, user requirement and stage wise methodology of plant design and selection.
- Summary of evaluation of various process alternatives as a record for further verification of finalised process.
- Heat and Material Balance Data including simulation of process at preliminary stage for deciding and sizing of equipment
- Preliminary Process Flow Diagrams (PFDs) including understanding what exactly PFD is, why it is required, who are the users, what is purpose, what type of inputs are required, how to use the inputs for preparation of PFD, how to check prepared PFD and method of maintaining IDC (Inter Department Checking) records.
- Equipment List including their service conditions based on experience and as per available vendor data which is used by Equipment department for finalising vendors and further detailed engineering. List of equipment is also used by piping department for development of preliminary plot plan and basic equipment layouts. Equipment list also is used by other engineering disciplines like Electrical, Instrumentation and Civil/Structural including some vendors.
- Approximate Capex and Opex based on preliminary process based on equipment list.
- Raw Material Requirement based on preliminary process data
- Utilities requirement based on preliminary process data for finalising vendors
- Risk summery at various stages like plant running condition, maintenance etc… This completes PRE-FEED activities
- Module 4 : FEED or Basic Engineering Package including Deliverables
-
- Project Phase 3 – Process Design Package with Deliverables
-
- Raw material specifications
- Plant capacity requirements
- Product specifications
- Critical plant operating parameters
- Available utilities specifications
- Individual unit operations performance requirements
- Process regulatory requirements
- All other operating goals and constraints desired by the plant owners/operators/engineers.
- Process design basis
- Material & Energy Balance (M&EB)
- Process Flow Diagrams (PFDs) of Tanks, Vessels, Reactors, Distillation Columns, Absorption Columns, Phase Separators, Condenser, Sub-coolers, Heat Exchangers, Pumps, Compressor, Turbines, Blower etc…
- Process descriptions
- Utility balances and Utility Flow Diagrams (UFDs) like Steam, Chilled Water, Cooling Water, Nitrogen, Instrument Air, Compressed Air, Plant Air.
- Piping & Instrumentation Diagrams (P&IDs) of Tanks, Vessels, Reactors, Distillation Columns, Absorption Columns, Phase Separators, Condenser, Sub-coolers, Heat Exchangers, Pumps, Compressor, Turbines, Blower etc…
- Process control description
- Preliminary line/pipe list of all prepared P & ID
- Process Equipment List and Preliminary instrument list, and Preliminary Tie in list
- Equipment process datasheets of Tanks, Vessels, Reactors, Distillation Columns, Absorption Columns, Phase Separators, Condenser, Sub-coolers, Heat Exchangers, Pumps, Compressor, Turbines, Blower etc…
- Instrument process datasheets of Pressure Instruments, Temperature Instruments, Level Instruments and Flow Instruments.
- Hydraulic design reports.
- Preliminary general arrangement drawings including building requirement and general description of project site
- Budget pricing from vendors on major pieces of equipment
- Process design philosophies
- Relief system design basis and Relief scenario datasheets and relief valve process datasheets
- Material Selection Diagrams (MSDs) and piping specifications
- Tie-in list and Process specialty items list
- Identification of power source and location and Preliminary single line diagrams
- Raw material and product storage and handling requirements
- Process effluent and emissions summary
- Process risk analysis (PHA, HAZOP, etc.) and Preliminary operating procedures
- Preliminary product and in-process QC sampling/testing plan and Preliminary project schedule. This stage completes FEED Package or Basic Engineering Package.
- Detailed mass and energy balances
- Unit operation design/evaluation
- Piping system hydraulics calculations
- Relief and flare system design/evaluation
- Heat exchanger design/evaluation
To enhance skills of Chemical / Process engineers to explore, economically feasible and ecologically sustainable process know how
Enquiry Now
Upcoming Batches
FAQ's
What is process engineering?
Process engineering involves the design, optimization, and operation of industrial processes for the production of various products. It focuses on the development and implementation of efficient and safe processes in industries such as chemical, petrochemical, pharmaceutical, food and beverage, and oil and
gas.
What topics are covered in a process engineering course?
Process engineering courses typically cover subjects such as chemical engineering principles, mass and energy balances, fluid mechanics, heat transfer, chemical reactions and kinetics, process control, process
equipment design, process safety, and process optimization.
What are the career prospects for process engineers?
Process engineers have diverse career pportunities in industries such as chemical manufacturing, oil and gas refining, pharmaceuticals, food and beverage production, environmental engineering, and more. They can work as process engineers, production engineers, plant managers, process control engineers, research
and development specialists, or in related roles.
What job opportunities are available for process engineering graduates?
Process engineering graduates can find job opportunities in a wide range of industries such as chemical manufacturing, oil and gas, pharmaceuticals, food and beverage, environmental engineering, and more. Some common job roles include process engineer, production engineer, plant manager, process control
engineer, research and development specialist, and process safety engineer.
How is the job market for process engineering graduates?
The job market for process engineering graduates can vary based on factors such as industry demand,
economic conditions, and geographical location. However, process engineering is a crucial field in many industries, and there is generally a demand for skilled process engineers.
What skills are employers looking for in process engineering graduates?
Employers typically seek process engineering graduates with strong technical skills in areas such as process design, process optimization, process control, and safety. Additionally, skills in process simulation software,
data analysis, problem-solving, teamwork, communication, and project management are highly valued.
Are there any placement assistance services provided by SIT?
We have a dedicated Placement cell which continuously seeks for employment opportunities and arranges
On-Campus as well as Off-Campus recruitment activities. The institute assists students to enter in their respective industries by providing 100% Placement assistance. The Placement Cell conducts Mock Interviews of students for their preparation for final interviews in the industry.
Testimonials
I have completed my PGD in Piping Engineering from the Suvidhya Institute of Technology (Batch-140).
I feel very gratified that I am part of SIT. The overall experience was very remarkable we were given in-depth knowledge of the subject as well we were thought interpersonal skills. The teachers of the institute are highly skilled and are extremely helpful and always ready to assist you with your doubts. As the world is facing COVID 19 pandemic, the institute didn't pause our training however the whole training was launched online and was as good as the classroom program.
The one thing that inspired me and make SIT distinct from other institutes is their regular Assignment and Tests which keeps students well on track of the subject. If someone is thinking to pursue PGD in Piping Engineering from Suvidhya Institute of Technology I would highly recommend providing he/she must be eager to study the subject. I would like to thanks all faculty of SIT especially Mr.Vasant Mestry Sir for his immense efforts and making us ready for our future endeavours.
Mehmoodkhan Roshankhan DalwaiBatch No.01140,Piping Engineering I feel very gratified that I am part of SIT. The overall experience was very remarkable we were given in-depth knowledge of the subject as well we were thought interpersonal skills. The teachers of the institute are highly skilled and are extremely helpful and always ready to assist you with your doubts. As the world is facing COVID 19 pandemic, the institute didn't pause our training however the whole training was launched online and was as good as the classroom program.
The one thing that inspired me and make SIT distinct from other institutes is their regular Assignment and Tests which keeps students well on track of the subject. If someone is thinking to pursue PGD in Piping Engineering from Suvidhya Institute of Technology I would highly recommend providing he/she must be eager to study the subject. I would like to thanks all faculty of SIT especially Mr.Vasant Mestry Sir for his immense efforts and making us ready for our future endeavours.
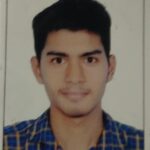
I have been completed Piping engineering Course from suvidya Institute (Batch 140). I feel it is the best place to acquire practical industry oriented skills.Our course is designed as per industry need. Assignments which are taken during course are very usefull to experience actual work in industry and that's the speciality of SIT.... Our teaching and non teaching staff are good. In this institute not only therotical but also practical knowledge is shared and which are very helpful to everyone... Even in this covid 19 pandemic topics are covered by online. Our trainer Mr.Vasant Mestry sir is the expert in this field who taught us life skills along with Piping Engineering which helps to turn ourself into a better individual. I feel lucky to be a part of SIT family. Thanks to SIT family...
Auti Omkar Savleram Batch No.01140, Piping Engineering 
Previous
Next